
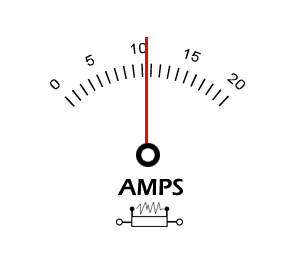
The torque for the combined motors (2.1 x 5250) / 7000 equals 1.575 ft-lb, however the RPM has increased from 3,450 to about 7000 RPM. The torque for the first motor is easily calculated using the formula ( hp x 5250)/RPM …. This has been made possible due to way in which the RPM has been increased and accumulated, however combining the motors, the efficiency goes down somewhat to 0.78 (0.885 x 0.885), or a combined hp of 2.1hp (0.78 x 2.68hp). In addition to the accumulated RPM, the hp from both motors has also been aggregated. In a linear operational amplifier, the output signal is the amplification factor, known as the amplifiers gain ( A ) multiplied by the value of the input signal and depending on the nature of these input and output signals, there can be four different classifications of operational amplifier gain.

This increase in RPM is not due to either modulation of frequency or by using different sized pulleys/gears. The combined RPM of about 7,000 is evidenced on the rotor of the second motor. The RPM from the first motor (3,450) is transferred to the second motor, and then aggregates with the RPM from the second motor. The prototype contains two modules for proof of concept.
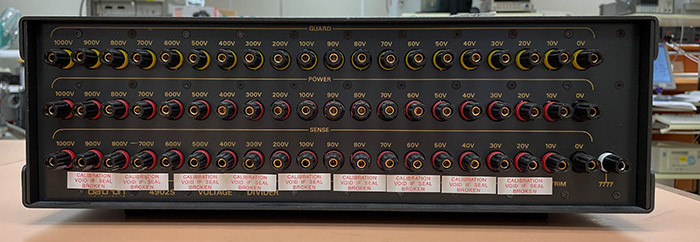
We have just completed a working prototype that is comprised of two 1000W (1.34 hp each) induction type motors, which based on an efficiency of 0.885, equals to 1.18hp net for each motor. Please comment on the following including if possible potential commercial applications.
Amp to volt ratio portable#
On average these are fairly loud as compared to an induction motor, and there will be sparks from the brushes (and the brushes wear and need to be replaced) but they are a common approach to getting high speed operation, as seen in most portable saws, drills and routers, or small hand-held rotary tools.įor an application requiring a fixed 7000 or 7200 RPM speed, a simple belt & pulley arrangement to double the motor shaft speed is likely to be the most cost-effective and power efficient approach (gearboxes are relatively expensive and can also be surprisingly inefficient.) The other common option for higher-speed motors is not an induction motor - rather a brushed type DC or universal motor. On 60 Hz its 3600, 18 - on 400 Hz its 24,000, 12,0.Ī variable frequency drive can provide a wide range of speeds, but it can also provide more speed than a motor may be designed for - if a motor purely intended to run on 60 HZ is attached to a VFD and wound up to 120 Hz, you might find the mechanical limits of strength in the rotor and destroy it (loud noises, sudden stops, great expense.) There are motors specifically made for VFD operation which are rated for higher operation speeds - while expensive as compared to a normal motor, they are cheap as compared to what can happen when a normal motor comes apart in use. Induction motor speed is a matter of poles and frequency - on 50 Hz you'll get 3000, 1500, 1000 as you go from 2-pole to 4 pole to 6 pole.
